Liquid silicone (LSR) is a high-quality silicone
that offers a wide range of applications in many industries.
Why Choose Liquid Silicone (LSR)?
Consider liquid silicone rubber (LSR) when choosing materials for the manufacture of parts and components. Liquid silicone is the basic material that we process at GGF TMRubber. The chemical properties of liquid silicone rubber make it an ideal material for applications spanning several different industries.
What is liquid silicone (LSR)
LSR liquid silicone is used in many industries. It is most often used in construction, electronics, automotive, as well as in the medical and food industry.
What’s so special about this revolutionary material? LSR is a form of silicone made of two components. It is characterized by high purity, which makes it suitable for a wide range of applications where mechanical strength is a prerequisite, along with the need for the highest chemical resistance and unsurpassed quality.
The unique physical properties of silicone rubber are due to its chemical structure. Silicone rubber is an elastomer consisting mainly of a chain of molecules known as a siloxane bond (-Si-O-Si-). This chain is an effective „backbone” of silicone rubber, to which various organic chemical groups can be added, changing its mechanical and material properties.
Silicone rubber is distinguished from other elastomers by the strength of its siloxane bond. While the carbon bonds have a bond energy of 355 kJ / mol, the strength of the siloxane bond is 433 kJ / mol. This contributes to its greater heat resistance, chemical stability and electrical insulation.
At the same time, siloxane bonds are also characterized by low intermolecular forces, which means that other chemical groups attached to them are free to rotate. For this reason, liquid silicone rubber has material properties such as a high degree of flexibility and compressibility, as well as water resistance and good release ability.
Mechanical properties of silicone (LSR)
Different grades of silicone rubber have different material properties. This versatility is one of the reasons the LSR is used in so many different applications.
Whether you need a medical or food product that offers excellent bacterial resistance or an automotive component that can withstand excessive heat and vibration, the mechanical properties of liquid silicone make it an excellent starting point.
You can use the LSR in temperatures from -40˚C to 250˚C, expose it to wind, rain and UV light for long periods, or submerge in water, oil or solvents. Different grades of LSR have different material properties to meet even the most demanding applications.
The key properties of silicone rubber material include:
- quick hardening and low compression ratio,
- resistance to tearing, high temperature, water and oil,
- transparency and electrical conductivity
- overall strength and long life.
Wide temperature range
Liquid silicone products have a wide temperature range. They do not lengthen at high temperatures. They also remain flexible at temperatures down to -40˚C. High thermal stability makes LSR parts suitable for heavy duty applications.
Chemical stability
Liquid silicone components are chemically inert, hypoallergenic and resistant to bacterial growth. They are also characterized by high biocompatibility, which makes them suitable for medical applications. However, they can be degraded under the influence of some organic compounds or a strongly acidic or alkaline environment.
Electrical resistance
LSR itself offers high resistance to corona discharge, making it a good choice for use as an insulator in high voltage applications. However, it is also possible to add conductive materials without compromising other properties of the LSR component, so that it can be used to create contact points for the keyboard and other electrical parts.
Endless possibilities of silicone (LSR)
The growing popularity of LSR products can be explained by the range of unique properties. They result from the chemical structure of the compounds, which is based on a set of strong siloxane bonds that are more stable and offer higher strength compared to carbon bonds.
These properties of LSR cover a spectrum of needs, making it a versatile compound for many applications.
First, LSR compounds are extremely durable and resistant to extreme temperatures and environments. These materials provide functionality at temperatures ranging from -40 ° C to 250 ° C. LSR compounds do not stretch even at high temperatures and remain flexible in the cold.
LSR compounds are strong, flexible and stable, offering excellent performance over a long period of time. They can be electrical and thermal insulators, ensuring excellent conductivity preservation.
These compounds are highly inert, biocompatible and hypoallergenic, meaning that they can be applied to components that come into close contact with the human body, such as prostheses and artificial organs. However, these compounds may degrade in contact with an alkaline or strongly acidic environment – this should be taken into account.
LSR blends can be produced in any color possible due to the transparency of the material, which is then pigmented to blend in with any shade required. The LSR can even be colored to suit a wide spectrum of human skin tones.
From a production perspective, LDS components can be produced in large volumes, with short cycle times, automated processes and little waste.
Molded LSR elements are tasteless and odorless. These parts are used in many different settings. Other key properties of this versatile material include:
- Flame retardant
- Intensive resistance to weather conditions
- Resistant to steam and moisture
- Absorbs vibrations
- Corrosion resistant
- Mildew resistant
• Resistant to UV radiation
So it’s easy to see why LSR products have become so popular in so many industries. LSR compounds are useful in the medical, cosmetic and food industries because they are non-reactive and non-toxic.
In the automotive industry, their heat resistance makes them ideal for use close to engines. They are useful in any application related to electricity. LSR compounds are also ideal for the production of products consisting of complex parts that must be manufactured at high speeds without sacrificing precision and for the highest productivity.
Quite simply, LSR is a material that can be used in a myriad of applications – provided you consult industry experts about its suitability and manufacturing. This last point is important – the LDS is not for everyone, despite its myriad uses and benefits. An injection molding expert can tell you when LSR is the best mix for your project.
GGF TMRubber will help you decide in which direction your production should go.
Liquid silicone applications (LSR)
The LSR is so versatile you’ll find it in many different places. New applications for this material are discovered every day. We are well versed in how to get the most out of the LDS. Many companies in the medical, automotive, electronics and hardware industries are already using the LSR, and you can too.
Common LSR products include:
- joints and membranes;
- wide range of gaskets and gaskets, including o-rings; parts of the catheter, including the tubing;
- hand tools;
- keyboard buttons and backlit buttons, valves;
- soft-touch surfaces and keys;
- steam sterilized parts; valve components;
- and many other applications.
LSR är så mångsidig att du hittar den på många olika ställen. Nya tillämpningar för detta material upptäcks varje dag. Vi är väl insatta i hur man får ut det mesta av LRS. Många företag inom medicin-, fordons-, elektronik- och hårdvaruindustrin använder redan LSR, och du kan också.
Vanliga LSR-produkter inkluderar:
- skarvar och membran;
- brett utbud av packningar, inklusive o-ringar; delar av kateter, inklusive slangen;
- handverktyg;
- tangentbordsknappar och bakgrundsbelysta knappar, ventiler;
- mjuka ytor och nycklar;
- ångsteriliserade delar; ventilkomponenter;
- och många andra applikationer.

Two-component grades of silicone rubber
The liquid silicones we use are two-component grades of silicone rubber that can be injection-molded on fully automatic machines without the need for secondary processing.
They generally vulcanize with a platinum catalyst and vulcanize under the influence of heat and pressure.
As a rule, component A contains a platinum catalyst, while component B consists of a crosslinking agent. They are ideal for high-volume production, thus helping to reduce unit costs.
Liquid silicone offers a wide range of industrial applications:
- Healthcare and medical technology
- Mechanical and plant engineering
- Electrical engineering
- Transmission and distribution cables (T&D)
- Construction
- Consumer goods and the food industry
- Automotive
Liquid silicone (LSR) in the automotive industry
Especially for applications in the automotive industry, we offer the FLR series of fluorine silicones, which are characterized by particularly high stability against aggressive media such as gasoline, engine and gear oils. They are mainly used in the production of automotive and aviation seals.
Adhesive grades of liquid silicone rubber are particularly preferred, which bond to many plastics and metals without undercoating or physical pre-treatment, can be used for multi-functional parts such as hard-soft combinations and membrane components.
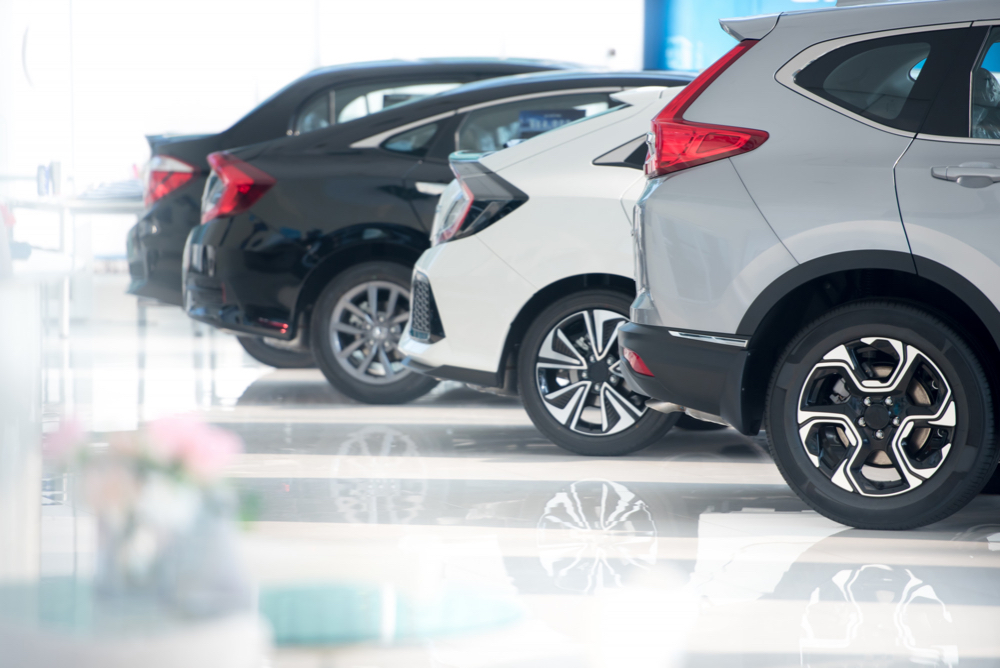
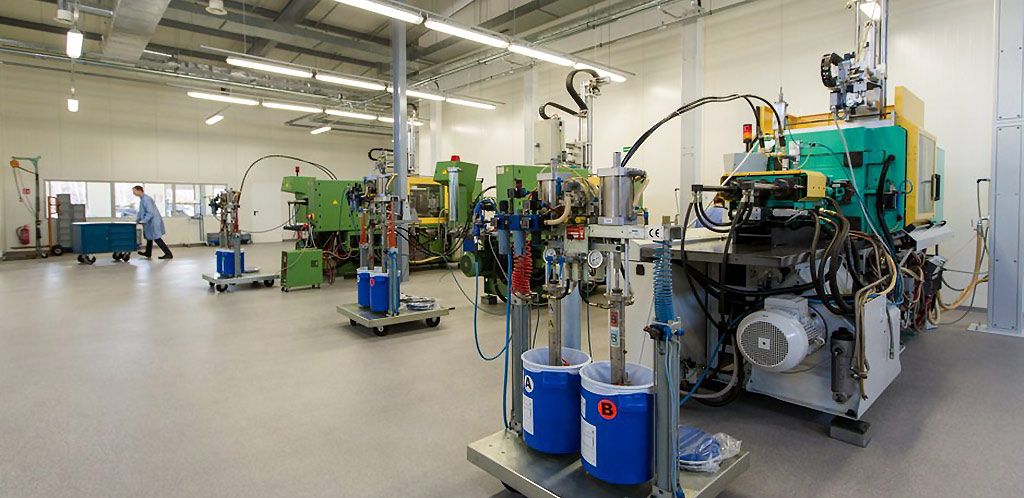
Processing of LSR liquid silicone
Liquid silicone is processed by injection. Using injection molding, we can produce components with complex geometric shapes and precise dimensions in a fully automated production configuration without the need for secondary processing.
Some of the liquid silicones also contain special viscosity-lowering additives that are suitable for coating technical textiles as they do not require high pressure curing. This allows the positive properties of silicone elastomers, such as heat and flame resistance, to be combined with the high mechanical strength of traditional technical textiles.