Pressing is a manufacturing process in which a metered amount of molding material, which is usually preheated (usually referred to as batch), is pressed into the desired mold using two heated molds.
Press molding is used in a wide range of applications. Solid silicone rubber is vulcanized in the molds by temperature and pressure. Preferred solid silicone processing processes for compression pressing and transfer pressing.
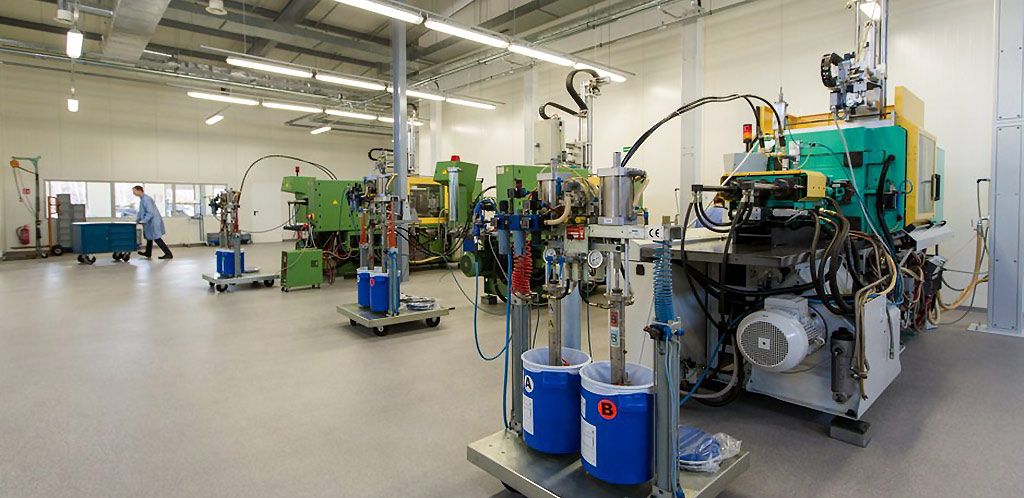
Compression moulding
Material selection / Seat filling
For compression pressing, silicones cross-linked with peroxides or with a platinum catalyst are preferred.
Each slot is individually filled with a precisely measured amount of silicone.

Compression and vulcanization
Processing presses are usually hydraulically controlled, press plates are usually electrically heated, less steam heated. For the vulcanization of silicones cross-linked with peroxide catalysts or a platinum catalyst, temperatures of 150 to 200 ° C are used. Correct temperature plays an important role: it should be as high as possible to shorten cure time and cycle time. At the same time, it must not be too large to avoid scorching. The vulcanization time is determined by the material temperature, the mold temperature and the wall thickness of the produced detail.
Removal of the molding
To facilitate removal of the molded parts from the mold cavities, external or internal release agents can be used.
- External agents, in the form of a spray to spray onto the mold surface.
- Internal measures in the form of special silicone additives.
Pay attention to the correct dosage of the release agents. Too much can contaminate the mold cavities by depositing on the hot mold wall. It can also cause inhomogeneities in the finished product. When excess release agent is forced through the flow of material while filling the cavity, it can lead to unwanted seam lines due to incomplete fusing of the two flowing jets. In either case, the end product may not be serviceable.
Transfer compression
Transfer ironing is an extension of the compression pressing process. It is more economical for small details of complex shape that are produced in large numbers.
In transfer pressing, unvulcanized silicone is put into a special chamber, usually located in the upper part of the mold. Then, when closing the mold, the material pressed by the cylinder located in the upper half of the chamber is forced through the gating channels to the seats.
